PredictionofDynamicMaterialFailure:GISSMOinLS-DYNA
2016-09-26 by:CAE仿真在線 來源:互聯(lián)網(wǎng)
材料失效動態(tài)預(yù)測Part II: GISSMO模型在LS-DYNA中的應(yīng)用
摘要


A Generalized Scalar Damage Method (GISSMO)1Introduction? For forming simulations, a more sophisticated and anisotropic description of yield loci – often based on the Hill or Barlat (1989) criteria – is considered important, which makes it necessary to use different constitutive models for both parts of the process chain. ? A damage model suitable to be used for both disciplines therefore has to be able to correctly predict damage regardless of the details of the constitutive model formulation.? To fill this gap the damage model GISSMO (Generalized Incremental Stress-State dependent damage MOdel) has been developed at Daimler and DYNAmore (Neukamm et al. (2009), Haufe et al. (2010)). ? It combines proven features of damage and failure description available in crashworthiness calculations with the possibility of mapping various history data from sheet metal forming to final crash loading.
2GISSMO – a short description? GISSMO = Generalized Incremental Stress State dependent damage MOdel ? Separate treatment of plasticity formulation and damage/failure prediction? To be combined with arbitrary constitutive models, e.g. *MAT_024 (von Mises)? Coupling of damage to stresses pFailure strain in dependency of triaxiality ? triaxiality η:quotient of mean stress and von Mises-stress
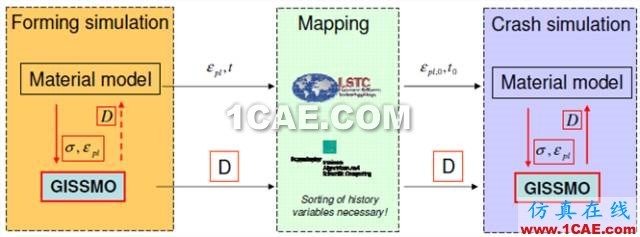
3Different ways to realize a consistent modeling


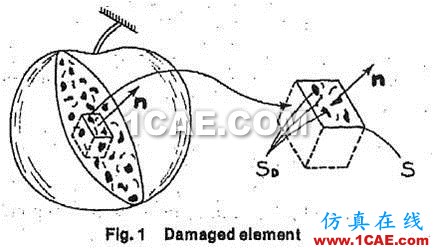
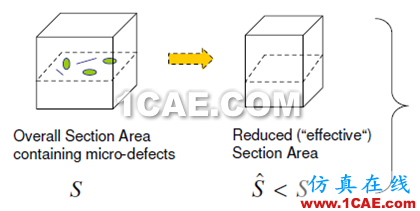
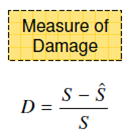

2GISSMO – a short description Ductile damage and failure The input of this failure strain is realized as a tabulated curve definition of failure strain values vs. triaxiality.
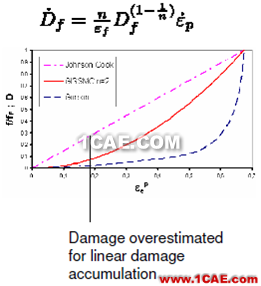
Damage Evolution
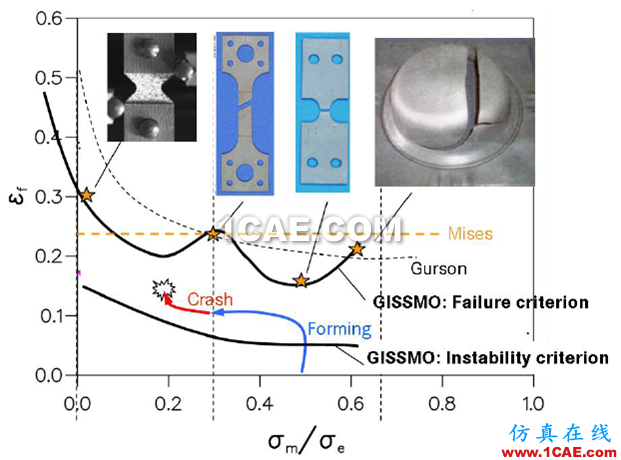
Failure Curve

3Failure criterion for Shell vs. Solid
Currently, modeling with shell elements is the main stream practice in crash safety simulation.
However, to predict crack initiation and propagation in detail, we need a modeling methodology with fine solid elements.
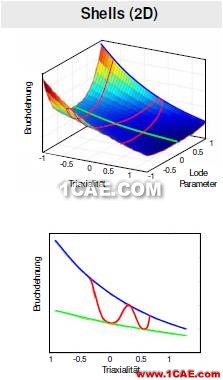
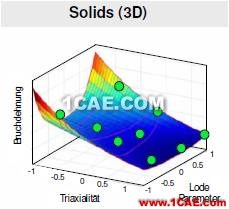
? For shells (2D with the assumption of plane stress ) triaxility and Lode angle depend on each other.
fracture strain is a function of the triaxiality
? For Solids (3D) both the Lode angle and triaxiality are independent fracture strain is a function of triaxiality and Lode angle
By increasing the thru-thickness integration points, one can increase the resolution to monitor the progress of damage.
? When stress in an element reaches its element erosion state
solid model will remove element. This step will form a cut (surface) or void (internal) and create a local stress concentration or even singularity within the model (color red), which may propagate either in thru-thickness or in-plane direction.
Unlike its shell approximation counterpart, it can only suppress one of its (Gaussian) integration point, weakening the structure locally but not enough to create geometrically singular feature.
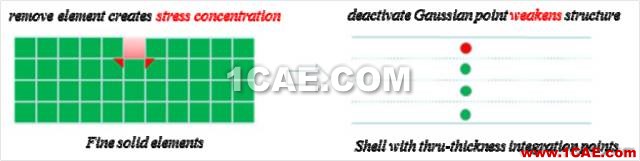

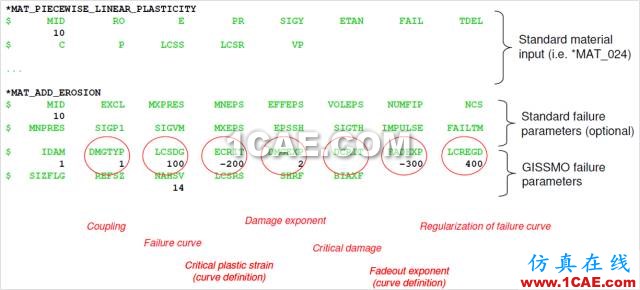
Summary
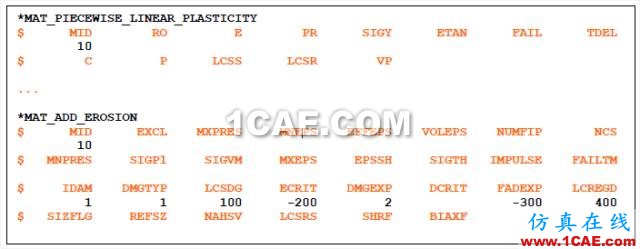




Q & A


相關(guān)標(biāo)簽搜索:PredictionofDynamicMaterialFailure:GISSMOinLS-DYNA ls-dyna有限元分析培訓(xùn) ls-dyna培訓(xùn)課程 ls-dyna分析 ls-dyna視頻教程 ls-dyna技術(shù)學(xué)習(xí)教程 ls-dyna軟件教程 ls-dyna資料下載 ansys lsdyna培訓(xùn) lsdyna代做 lsdyna基礎(chǔ)知識 Fluent、CFX流體分析 HFSS電磁分析