【優(yōu)秀論文】基于 OptiStruct 的白車身拓?fù)鋬?yōu)化研究
2016-11-28 by:CAE仿真在線 來源:互聯(lián)網(wǎng)
基于 OptiStruct 的白車身拓?fù)鋬?yōu)化研究
Study on Topology Optimization of Body-in-white Based on OptiStruct
張繼游
(吉利汽車研究院 杭州 311228)
摘 要:本文以柔度最小化為目標(biāo)建立了汽車白車身拓?fù)鋬?yōu)化模型,采用的優(yōu)化工具為 OptiStruct, 分析工況包括彎曲剛度、扭轉(zhuǎn)剛度、正面碰撞、后面碰撞和側(cè)面碰撞,目的是考察拓?fù)鋬?yōu)化技術(shù)在車 身架構(gòu)前期開發(fā)中應(yīng)用的可行性。
關(guān)鍵字:白車身 拓?fù)鋬?yōu)化 加權(quán)柔度 OptiStruct 載荷傳遞路徑
Abstract: This paper presents a mathematical method for topology optimization of vehicle Body-in-white (BIW) to minimize the structural compliance with several load cases including bending stiffness, torsion stiffness, frontal crash, rear crash, and side crash based on OptiStruct. The purpose is studying the feasibility of topology optimization techniques applied on vehicle architectures in early research and development.
Key words: Body-in-white, Topology Optimization, Weighted Compliance, OptiStruct, Load Paths
1 概述
中國汽車自主品牌經(jīng)過近十多年的發(fā)展,開發(fā)水平從早期的抄襲模仿,逐步轉(zhuǎn)向正向設(shè)計,車型 研發(fā)的領(lǐng)域逐步提前到前期開發(fā)階段。在車身架構(gòu)的前期開發(fā)階段,可以利用拓?fù)鋬?yōu)化技術(shù)探索載荷 傳遞路徑,從而為后期的工程開發(fā)提供合理的車身架構(gòu)[1-2],避免出現(xiàn)重大的設(shè)計失誤,同時降低設(shè) 計成本,提高研發(fā)速度。本文根據(jù)某車型的上一代車身架構(gòu),在 HyperMesh 中建立拓?fù)鋬?yōu)化模型, 利用拓?fù)鋬?yōu)技術(shù)獲取前期車身架構(gòu),拓?fù)鋬?yōu)化工具采用 OptiStruct 求解器,目的是考察拓?fù)鋬?yōu)化技術(shù) 在車身架構(gòu)前期開發(fā)中應(yīng)用的可行性。
2 模型描述
根據(jù)某車型的上一代白車身有限元模型(如圖 1 所示),建立白車身拓?fù)淠P?如圖 2 所示), 由于水箱橫梁總成對本次拓?fù)鋬?yōu)化分析工況(剛度工況和碰撞工況)的影響較小,該部分總成沒有建 立拓?fù)淠P?。考慮到整車在前后碰撞過程中需要縱向剛度比較好,因此將前后縱梁總成直接設(shè)定為非 設(shè)計空間,其余網(wǎng)格均作為設(shè)計空間。為了方便優(yōu)化過程控制,分為若干區(qū)域并分別賦予不同的屬性, 再施加約束和載荷,建立拓?fù)鋬?yōu)化的有限元模型,如圖 2 所示。

圖 1 白車身有限元模型 圖 2 白車身拓?fù)淠P?
3 拓?fù)鋬?yōu)化
3.1 優(yōu)化目標(biāo)與約束
本研究的優(yōu)化的目標(biāo)為各個工況下白車身的柔度最小化,設(shè)計變量為單元密度,約束分別是體積 分?jǐn)?shù)、單元最小尺寸約束、對稱約束和拔模約束。其中,體積分?jǐn)?shù)是指當(dāng)前迭代步設(shè)計空間體積與初 始設(shè)計空間體積的比值,而對稱約束是指相對于車身 XZ 平面,車身結(jié)構(gòu)左右對稱,車身地板、頂棚、 B 柱和防火墻部件的單元添加拔模約束。
白車身拓?fù)鋬?yōu)化工況包括剛度工況和碰撞工況。其中,剛度工況包括彎曲剛度工況和扭轉(zhuǎn)剛度工 況,碰撞安全工況包括正面碰撞工況、后面碰撞工況和側(cè)面碰撞工況。碰撞工況對車身的影響都是大 變形、非線性的,還有接觸力存在。目前拓?fù)鋬?yōu)化與有限元方法相結(jié)合的方法并不成熟,尤其針對白 車身拓?fù)鋬?yōu)化問題,因此必須將這類非線性工況等效為線性工況。本研究在 HyperMesh 前處理工具 中建立上述拓?fù)鋬?yōu)化工況,并采用 OptiStruct 求解器進(jìn)行拓?fù)鋬?yōu)化,最后用 HyperView 后處理工具進(jìn) 行拓?fù)鋬?yōu)化結(jié)果分析。
一般來說,不同的載荷工況將得到不同的結(jié)構(gòu)拓?fù)?。傳統(tǒng)的多目標(biāo)優(yōu)化問題采用線性加權(quán)和法, 將多目標(biāo)問題轉(zhuǎn)化為單目標(biāo)問題求解,但對于非凸優(yōu)化問題來說,該方法不能確保得到所有的 Pareto 最優(yōu)解。本研究多目標(biāo)拓?fù)鋬?yōu)化采用的方法是折衷規(guī)劃法(Compromise Programming Approach)[3]。 多工況拓?fù)鋬?yōu)化的數(shù)學(xué)方程如下所示:
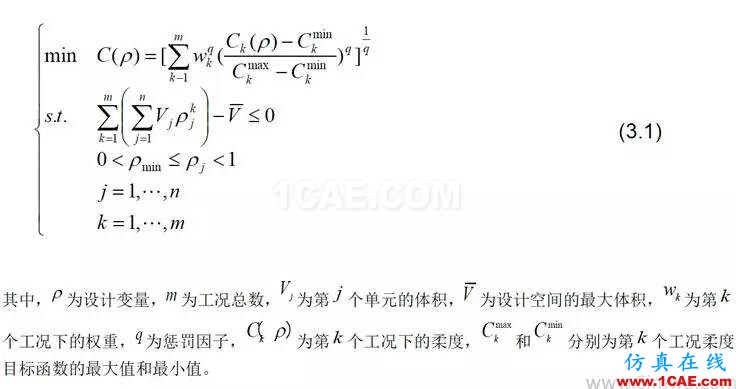
3.2 各個工況優(yōu)化結(jié)果分析
(1)彎曲剛度工況
彎曲剛度工況優(yōu)化結(jié)果如圖 3 所示。柔度經(jīng)過 34 迭代,最終優(yōu)化的最小柔度為 13.9N?mm,迭 代過程如圖 4 所示。由圖 5 可知,載荷傳遞路徑有 3 條,中央通道下橫梁①→前縱梁末端②,中央通 道下橫梁①→門檻梁③,備胎前橫梁④→后縱梁中部⑤。
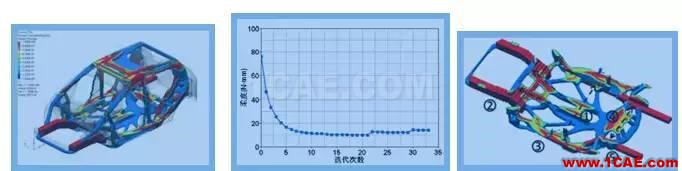
圖3 彎曲剛度工況優(yōu)化結(jié)果 圖4 柔度迭代過程 圖5 優(yōu)化結(jié)果解析
(2)扭轉(zhuǎn)剛度工況
扭轉(zhuǎn)剛度工況優(yōu)化結(jié)果如圖 6 所示。柔度經(jīng)過 80 迭代,最終優(yōu)化的最小柔度為 97.7N?mm,迭 代過程如圖 7 所示。由圖 8 可知,材料在備胎前橫梁①和后橫梁堆積②,可知該兩個結(jié)構(gòu)對扭轉(zhuǎn)剛度 作用大,同時后縱梁中段前橫梁①通過載荷傳遞路徑與門檻梁③前端相連。
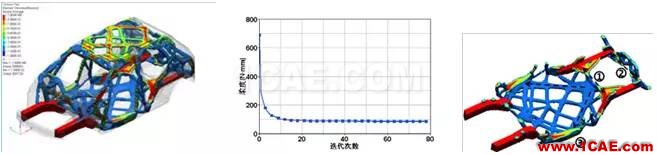
圖6 扭轉(zhuǎn)剛度工況優(yōu)化結(jié)果 圖7 柔度迭代過程 圖8 優(yōu)化結(jié)果解析
(3)正面碰撞工況
正面碰撞工況優(yōu)化結(jié)果如圖 9 所示。柔度經(jīng)過 25 迭代,最終優(yōu)化的最小柔度為 9KN?mm,迭代 過程如圖 10 所示。由圖 11 可知,載荷傳遞路徑由前縱梁中段①分叉,分別傳遞到上邊梁②和前縱梁 末端③,前縱梁末端③的載荷傳遞路徑又分為 3 條,分別是門檻梁④、前縱梁末端延伸段⑤和中央通 道下橫梁⑥。
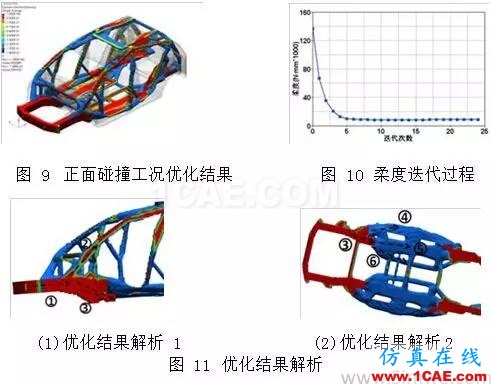
(4)后面碰撞工況
后面碰撞工況優(yōu)化結(jié)果如圖 12 所示。柔度經(jīng)過 31 迭代,最終優(yōu)化的最 ih 柔度為 29.5KN?mm, 迭代過程如圖 13 所示。由圖 14 可知,載荷傳遞路徑由后縱梁末段①分叉,分別傳遞到門檻梁②、前 縱梁末端延伸段③和中央通道下橫梁④。
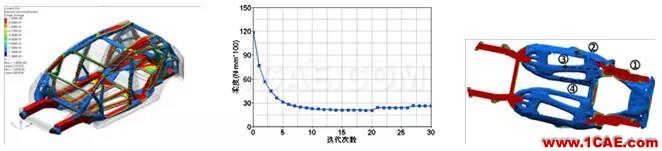
圖 12 后面碰撞工況優(yōu)化結(jié)果 圖 13 柔度迭代過程 圖 14 優(yōu)化結(jié)果解析
(5)側(cè)面碰撞工況
側(cè)面碰撞工況優(yōu)化結(jié)果如圖15所示。柔度經(jīng)過18 迭代,最終優(yōu)化的最小柔度為9.5KN?mm,迭 代過程如圖 16 所示。由圖17 可知,載荷傳遞路徑有 3 條,分別是門檻梁前端橫梁①、門檻梁中部橫 梁②和門檻梁末端橫梁③。
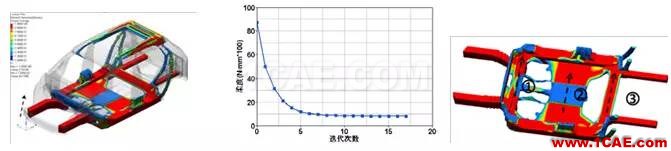
圖 15 側(cè)面碰撞工況優(yōu)化結(jié)果 圖 16 柔度迭代過程 圖 17 優(yōu)化結(jié)果解析
本研究通過對五個單獨分析工況進(jìn)行拓?fù)鋬?yōu)化,獲取各個工況的最佳材料分布和載荷傳遞路徑,載荷傳遞路徑上的零件,即為保證對應(yīng)工況性能要求的關(guān)鍵部件,為前期車身架構(gòu)設(shè)計提供指導(dǎo)意見, 將在后期的性能優(yōu)化中獲得重點關(guān)注。
3.3 綜合工況優(yōu)化結(jié)果分析
綜合優(yōu)化工況包括剛度工況(彎曲剛度和扭轉(zhuǎn)剛度)、碰撞工況(正面碰撞、后面碰撞和側(cè)面碰撞)。 對于每一種工況,都會有不同的拓?fù)鋬?yōu)化結(jié)構(gòu)與之對應(yīng),為了找到滿足各主要工況的拓?fù)浣Y(jié)構(gòu),本文采用折衷規(guī)劃法,參見公式(3.1),其中,
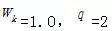
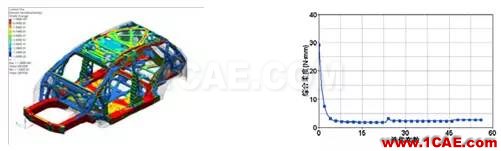
圖 18 綜合工況優(yōu)化結(jié)果 圖 19 加權(quán)柔度迭代過程
(1)地板優(yōu)化結(jié)果解析
由圖20 所示,橫向載荷傳遞路徑有4 條,分別是:前縱梁末端連接橫梁①、前座椅橫梁②、后縱梁前端連接橫梁④和后橫梁⑤;縱向載荷傳遞路徑有 1 條,即連接前縱梁末端連接橫梁①和后縱梁前端連接橫梁④的中央通道連接梁③,同時后橫梁⑤和后縱梁中段⑨通過斜梁⑥連接。
(2)頂棚優(yōu)化結(jié)果解析
由圖 21 所示,橫向載荷傳遞路徑有 3 條,分別是:頂棚前橫梁①、頂棚中橫梁②和頂棚后座椅 橫梁③,同時頂棚邊梁⑤通過 V 型梁④與頂棚后橫梁③連接。
(3)側(cè)圍優(yōu)化結(jié)果解析
由圖 22 所示,豎向載荷傳遞有 4 條件,分別通過上邊梁①、A 柱②、B 柱③和 C 柱④連接前后 縱梁/門檻梁⑤⑥⑦和頂棚邊梁⑧。
(4)防火墻優(yōu)化結(jié)果解析
由圖 23 所示,懸架支撐點④通過橫梁①連接,前縱梁后段⑤通過橫梁③連接,懸架支撐點④ 和 前縱梁后段⑤ 通過 V 型梁②連接。
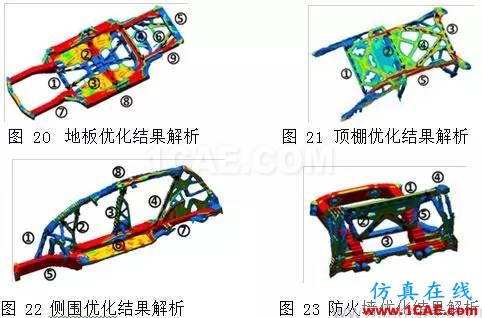
通過折衷規(guī)劃法, 綜合優(yōu)化工況兼顧各個分析工況的性能要求,拓?fù)鋬?yōu)化結(jié)果在滿足剛度和碰撞多學(xué)科性能的基礎(chǔ)上,實現(xiàn)最佳材料分布。設(shè)計人員可根據(jù)拓?fù)鋬?yōu)化結(jié)果,改進(jìn)原始車型的車身架構(gòu), 在車身結(jié)構(gòu)設(shè)計早期獲取滿足多學(xué)科性能的設(shè)計方案,從而加速車身開發(fā)速度,提升產(chǎn)品的競爭力。
4 結(jié)論
(1)本研究在 HyperMesh前處理工具中建立上述拓?fù)鋬?yōu)化工況,并采用OptiStruct 求解器進(jìn)行 拓?fù)鋬?yōu)化,獲取較為清晰的找到各個分析工況的載荷傳遞路徑。通過拓?fù)鋬?yōu)化,將材料分布的到最需 要加強的結(jié)構(gòu)上,極大提高了結(jié)構(gòu)的材料利用率,從而為后期的輕量化優(yōu)化提供最優(yōu)的車架拓?fù)浼軜?gòu)。
(2)本研究采用折衷規(guī)劃法進(jìn)行多工況拓?fù)鋬?yōu)化,消除了各個優(yōu)化工況的單位量綱差異,從而 獲得清晰的載荷傳遞路徑,并實現(xiàn)各個性能之間的權(quán)衡;本研究采用線性工況等效的方法來處理碰撞 工況,其拓?fù)鋬?yōu)化結(jié)果仍需要進(jìn)一步的驗證,未來將開展非線性拓?fù)鋬?yōu)化方法研究,例如靜載等效法(Equivalent Static Load)和混合細(xì)胞自動機法(Hybrid Cellular Automation)。
相關(guān)標(biāo)簽搜索:【優(yōu)秀論文】基于 OptiStruct 的白車身拓?fù)鋬?yōu)化研究 HyperWorks有限元分析培訓(xùn) HyperMesh網(wǎng)格劃分培訓(xùn) hyperMesh視頻教程 HyperWorks學(xué)習(xí)教程 HyperWorks培訓(xùn)教程 HyperWorks資料下載 HyperMesh代做 HyperMesh基礎(chǔ)知識 Fluent、CFX流體分析 HFSS電磁分析 Ansys培訓(xùn) Abaqus培訓(xùn)