重型車懸架系統(tǒng)靜強度及疲勞耐久性分析
2016-11-07 by:CAE仿真在線 來源:互聯(lián)網(wǎng)
1 引言平衡軸是懸架系統(tǒng)重要承力部件,在使用中出現(xiàn)局部斷裂,為了進一步找出其斷裂破壞原因,對懸架系統(tǒng)進行靜強度及疲勞分析,靜強度分析采用汽車行業(yè)功能強大的通用有限元分析軟件HyperWorks,疲勞分析采用FEMFAT5.0。圖1、圖2為整體式平衡軸斷裂后的照片。
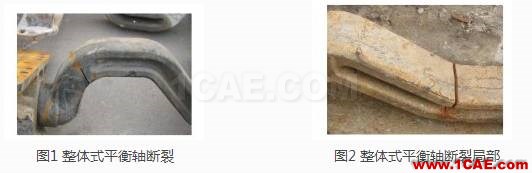
2 懸架系統(tǒng)分析有限元模型的建立

在HyperMesh中,選擇OptiStruct模板,截取部分車架總成模型,建立包括各相關(guān)零件的較為完整的分析計算模型。車架支撐板、縱梁、內(nèi)襯梁等板件采用四邊形和三角形二維殼單元,單元尺寸為10mm;鑄造橫梁、平衡軸支架、平衡軸采用四面體單元,單元尺寸為6mm。平衡軸支架通過螺栓連接固定在車架上;考慮平衡軸支架與平衡軸之間有2mm的間隙,在其接觸處采用1D里面GAP單元進行模擬。圖3所示為懸架系統(tǒng)有限元模型。

3 材料屬性和邊界條件

懸架系統(tǒng)分析有限元模型所對應(yīng)的材料屬性如表1所示。

表1 材料屬性
懸架系統(tǒng)各部件,根據(jù)具體的螺栓連接關(guān)系,采用Rbe2+Beam進行模擬,在車架前后兩端約束全自由度1,2,3,4,5,6 (1-X方向的平動自由度;2-Y方向的平動自由度;3- Z方向的平動自由度;4- X方向的轉(zhuǎn)動自由度;5- Y方向的轉(zhuǎn)動自由度;6-Z方向的轉(zhuǎn)動自由度)。平衡軸左右兩端均布沿Z向25噸均布力,平衡軸支架下端孔處沿X負方向集中力各3.375噸,重力加速度取g,如圖5所示為懸架系統(tǒng)分析有限元模型的約束和荷載示意圖。

4、靜強度計算結(jié)果分析

從以上計算結(jié)果(圖5-圖8所示)可以看出,平衡軸支架下端處最大位1.542,平衡軸左端軸線上翹0.207°,右端軸線上翹0.222°。平衡軸支架最大應(yīng)力為481.2MPa,安全系數(shù)為0.67;平衡軸最大應(yīng)力284.3,安全系數(shù)為1.13。平衡軸疲勞極限大小取為:0.5×強度極限=250MPa。由平衡軸應(yīng)力計算結(jié)果知,最大應(yīng)力及次大應(yīng)力均超過其疲勞極限,有發(fā)生疲勞破壞的危險,該位置與市場上支架出現(xiàn)斷裂的位置完全相同。
由以上分析,我們可以得出結(jié)論,市場上出現(xiàn)的平衡軸斷裂現(xiàn)象,主要是由于平衡軸所用材料屈服強度和抗拉強度過低,容易產(chǎn)生疲勞破壞所致,可考慮對平衡軸支架及平衡軸更換材料或改進結(jié)構(gòu),從而提高其強度安全性。
在FEMFAT5.0中,以懸架系統(tǒng)的應(yīng)力結(jié)果為疲勞應(yīng)力幅值,計算對稱應(yīng)力循環(huán)(即R=-1)時,對懸架系統(tǒng)進行疲勞分析,計算平衡軸支架和平衡軸的最小疲勞安全系數(shù)及疲勞壽命。如圖9-圖12所示。

經(jīng)過分析,平衡軸支架存在局部應(yīng)力集中部位,最小安全系數(shù)只有0.67;結(jié)合疲勞耐久性分析計算,支架最小疲勞安全系數(shù)為0.43,疲勞壽命為1.40×105次;平衡軸最小安全系數(shù)為1.13,最小疲勞安全系數(shù)為0.43,疲勞壽命約5.67×104 ,低于存活率達到99.9%條件下,零部件安全系數(shù)需達到1.32的要求。

5結(jié)論
文章結(jié)合某平衡軸支架斷裂的具體問題,采用HyperMesh11.0-RADIOSS建立了懸架系統(tǒng)有限元模型,進一步對懸架系統(tǒng)進行了靜強度和疲勞分析,找出了平衡軸支架斷裂的原因,并提出了有效的預(yù)防措施。
相關(guān)標(biāo)簽搜索:重型車懸架系統(tǒng)靜強度及疲勞耐久性分析 Ansys有限元培訓(xùn) Ansys workbench培訓(xùn) ansys視頻教程 ansys workbench教程 ansys APDL經(jīng)典教程 ansys資料下載 ansys技術(shù)咨詢 ansys基礎(chǔ)知識 ansys代做 Fluent、CFX流體分析 HFSS電磁分析 Abaqus培訓(xùn)